1. 서론
현대 기술의 발전과 함께 전자소자는 빠른 속도로 진화하고 있으며, 이 중에서도 특히 기존의 딱딱하고 부드럽지 않은 전자 소자와는 달리 유연한 소재와 구조를 가지는 유연전자소자는 다양한 방면에서 우리의 삶을 향상시켰다. 유연전자소자는 유연성과 신축성을 가져 제품의 디자인 자유도를 높여주며, 휴대성과 착용감을 개선하여 사용자의 편의성을 향상시키고, 내구성이 높아 충격에 강해 극한 환경에서도 신뢰성 있는 작동을 보장한다[1-3]. 또한, 유연전자소자는 조직과의 적합한 접촉과 낮은 기계적 응력과 같은 장점으로 인해 생체 신호 감지, 약물 전달, 신경 자극 등과 같은 다양한 용도의 체내 삽입형 의료소자 분야에서 사용되기에도 적합하다[4-7]. 이에 따라 유연전자소자가 많은 관심을 받아 활발한 개발이 이루어지고 있으며, 사용량의 증대 또한 기대되는 상황이다.
그러나 이러한 패치형 유연전자소자는 일회성으로 쉽게 사용되고 버려지며, 따라서 사용량 증가가 곧 폐기물 발생량의 증가로 이어져 토양 오염, 수질 오염, 공기 오염 등과 같은 환경 문제를 야기할 것으로 예상된다[8-10]. 따라서 환경 친화적이고 지속 가능한 해결책을 제시할 수 있는 생분해성 전자소자에 대한 관심이 많아지고 있다. 생분해성 전자소자는 생체액, 효소, 물 등 무해한 환경 조건에서 자연적으로 분해되는 생분해성 소재로 구성되어 있으며, 일정 기간 이후에는 환경과 인체에 해를 끼치지 않는 부산물로 분해된다. 이러한 소재는 폐기물의 양을 줄이고 재생 가능한 자원의 효율적인 사용을 도모하는 데 도움이 되기 때문에 지속 가능한 전자소자와 시스템을 개발하는 데 있어 매우 유망한 해결책으로 간주된다[11-13]. 생체 삽입형 의료소자에서도 생분해성 재료가 미래 재료로서 주목받고 있다. 기존의 삽입형 의료소자는 역할을 다한 후 소자의 제거를 위해 추가적인 수술이 필수적인 반면, 생분해성 의료소자는 스스로 분해되어 사라지기 때문에 제거 수술이 필요하지 않고, 이에 따라 수술에 따른 추가적 위험을 없앨 수 있다는 장점이 있다[14-17]. 이와 같이 생분해성 재료는 유연전자소자의 발전과 사용량 증대에 따라 잠재적으로 발생할 문제점들을 근본적으로 해결할 수 있다는 장점이 있으며, 이에 따라 생분해성 유연전자소자가 많은 주목을 받고 있다.
생분해성 전자소자의 제작 방법으로 생분해성 기능성 복합체를 인쇄하는 방법이 많은 관심을 받고 있다. 이는 기능성 재료와 고분자 매트릭스를 결합하여 복합체를 형성한 후 원하는 모양으로 소자를 인쇄하는 방법으로, 재료와 구조에 의한 기능성을 가짐과 동시에 우수한 기계적 특성을 제공한다는 장점이 있다[18-19]. 따라서 최근 많은 연구에서 생분해성 기능성 복합체를 활용하여 유연전자소자를 제작하려는 시도를 하고 있으며, 이러한 맥락에서 생분해성 기능성 복합체를 구성하는 다양한 재료들의 생분해 특성, 기계적 특성, 전기적 특성 등 구성 재료의 기초적인 물성뿐만 아니라, 기능성 재료를 고분자 매트릭스에 첨가함으로써 기능이 부여되고 강화되는 메커니즘, 첨가량에 따른 전기적 특성과 기계적 특성의 변화, 그리고 소자 작동 시간 및 소자 분해 시간 등에 대해 이해하는 것은 다양한 목적과 수명을 가지는 소자 제작과 활용을 가능하게 한다는 점에서 매우 중요하다[20-31]. 또한, 생분해성 복합체를 활용하여 얇고 가벼우며 통합성이 높아 부착형 전자소자에 적합한 2차원 전자소자, 혹은 복잡한 형태로 제작이 가능하며 체내 장기 모양에 맞춤형으로 제작 가능한 3차원 전자소자 등 다양한 구조를 가지는 소자를 제작할 수 있으며, 이에 따라 소자를 인쇄 및 제작하는 방법들도 많은 관심을 받고 있다[20-23, 28-29].
본 리뷰논문에서는 생분해성 기능성 복합체의 구조와 예시, 그리고 제작 방법과 활용 사례들을 소개한다. 생분해성 기능성 복합체에 대한 이해를 위해 구조와 구성 요소가 먼저 서술되며, 각 구성 요소들의 역할과 특성이 서술되었다. 생분해성 기능성 복합체의 종류로 전도성 복합체와 생분해성 유전체 복합체가 제시되며, 각 복합체의 기능성 부여 방식과 예시가 서술되었다. 다음으로 복합체를 활용한 다양한 전자소자 제작 방법과 활용 사례들에 대해 설명한다. 마지막으로, 현재의 한계점과 미래의 연구 방향과 전망에 대해 논의한다.
2. 본론
생분해성 기능성 복합체는 고분자 매트릭스, 기능성 필러, 그리고 가소제로 구성된다(Fig. 1(a)). 고분자 매트릭스는 기계적 특성과 생분해 시간에 주로 기여하며, 기능성 필러는 고분자 매트릭스에 기능을 추가하거나 강화하는 역할을 한다[19-21,25]. 필러로는 전도성을 부여하거나 유전체 특성을 강화하기 위해 무기 재료가 주로 사용되며, 필러의 양, 크기, 그리고 모양 등의 요소들에 따라 복합체 특성이 결정된다. 가소제는 기능성 필러들이 고분자 매트릭스 사이로 균일하게 분포할 수 있도록 함으로써 두 요소의 역할을 보조해준다[19-20,22]. 모든 구성 성분들은 생체액과 효소 등 다양한 인자에 의해 분해되는 특성을 가진다(Fig. 1(b)).
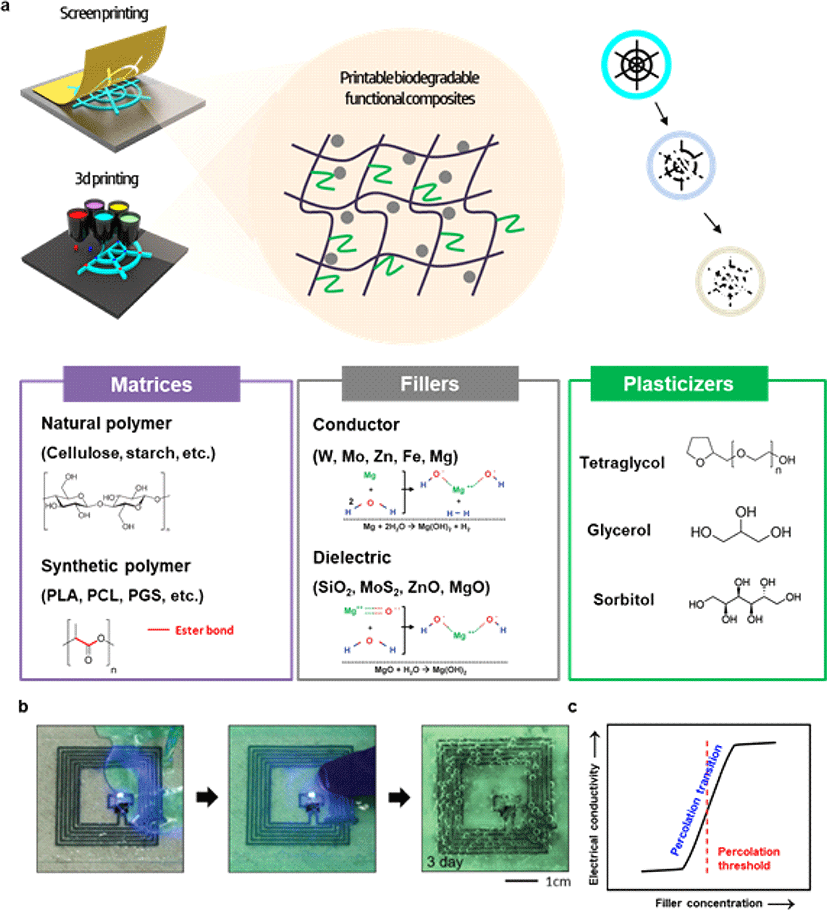
고분자 매트릭스는 복합체의 유연성, 신축성 등 기계적 물성을 결정하는 핵심 요소이며, 필러를 잡고 있는 바인더의 역할을 한다. 따라서 고분자에서 스웰링 및 분해가 일어나면 바인더의 역할을 못하게 되어 필러 손실이 일어나고, 이에 따라 필러 첨가에 의한 기능이 약화된다. 고분자 매트릭스는 천연 고분자와 합성 고분자로 분류된다. 천연 고분자는 셀룰로스(cellulose), 녹말(starch), 키토산(chitosan), 젤라틴(gelatin) 등 동물이나 식물로부터 추출되는 고분자로, 높은 생체 적합성과 생분해성을 가진다는 장점이 있어 많은 연구들에서 천연 고분자를 매트릭스로 사용하여 생분해성 기능성 복합체를 제작하였다[22,24-25,31]. Table 1은 현재 보고된 생분해성 기능성 복합체의 고분자 매트릭스로 사용되는 천연 고분자 물질들의 영률(young’s modulus), 연신율(elongation), 그리고 생분해 시간을 표로 정리한 것이다[32-43].
Polymers | Young’s modulus (MPA) | Elongation (%) | Degradation time |
---|---|---|---|
Cellulose | 20,000~30,000 [32] | 5~6 [33] | 95% loss in 10 weeks (in fallow soil) [34] |
Starch | 107.48 [35] | 25.625 [35] | 36 hours (in Cryptococcus flavs+YPM medium) [36] |
Chitosan | 110.86~116.54 [37] | 3.85~5.93 [37] | 50 wt.% loss in 6 hours (in 2 g lysozyme+1 mL PBS, 37°C) [38] |
Gelatin | 160~260 [39] | 12.5~14.58 [39] | 9~10 hours (in 0.1 mg lysozyme+1 mL PBS, 37°C) [40] |
Beeswax | 39 [41] | 17-21 [42] | 70~75 % loss in 80 days (in CO2 evolution test) [43] |
천연 고분자는 생체 적합성과 생분해성이 높다는 장점이 있지만, 내구성이 약하고 유연성과 신축 등의 기계적 특성을 설계하지 못한다는 단점 또한 존재한다. 이를 개선하기 위해 구조, 구성 및 고분자의 질량을 제어함으로써 필요한 기계적 특성을 제공할 수 있는 합성 고분자들이 개발되었다. 합성 고분자는 열에 대한 반응에 따라 열가소성 고분자와 열경화성 고분자로 구분된다. 열가소성 고분자는 열을 가해 온도를 녹는점 이상으로 높이면 액체 상태로 녹고, 온도를 충분히 낮추면 다시 고체 상태로 되돌아가는 반면, 열경화성 고분자는 열이 가해졌을 때 녹지 않고 경화되어 오히려 더 단단해지는 고분자이다. 열가소성 고분자에는 폴리부틸렌 아디페이트 테레프탈레이트(poly(butylene adipate-co-terephthalate, PBAT), 폴리카프로락톤(polycaprolactone, PCL), 폴리젖산(polylactic acid, PLA) 등이 포함되며, 열경화성 고분자에는 폴리언하이드라이드(poly-anhydride, PA), 폴리글리세롤 세바케이트(poly (glycerol Sebacate), PGS) 등이 포함된다[20-21,23,26,27-30,44]. 열가소성 고분자는 열에 의해 유연하게 만들 수 있다는 특징으로 인해 열경화성 고분자에 비해 상대적으로 공정이 쉽지만, 내열성이 떨어지는 특징을 보인다. Table 2는 현재 보고된 생분해성 기능성 복합체의 고분자 매트릭스로 사용되는 합성 고분자 물질들의 영률, 연신율, 그리고 생분해 시간을 표로 정리한 것이다[30,45-57].
Polymers | Young’s modulus (MPA) | Elongation (%) | Degradation time | |
---|---|---|---|---|
Thermoplastic | Poly(butylene adipate-co-terephthalate) (PBAT) | 40~50 [45] | 477~458 [45] | 10.14 wt.% loss in 5 days (in YCJ1 in soil) [46] |
Polycaprolactone (PCL) | 12.4~14.8 [47] | 142~242.4 [47] | 6 wt.% loss in 12 weeks (in PBS, 37°C) [57] | |
Polylactic acid (PLA) | 567~974 [45] | 8~12 [45] | 76 wt.% loss in 4 weeks (in PBS, 37°C) [48] | |
Poly(ethylene oxide) (PEO) | 1.6 [49] | 140~150 [49] | 10 mins (in water) [30] | |
Ploy (vinyl alcohol) (PVA) | 0.75~0.85 [50] | 70~130 [50] | 90 wt.% loss in 90 days (in PBS, 37°C) [51] | |
Poly(lactic-co-glycolic acid) (PLGA) | 2.37~3.03 [52] | 358.4~385.2 [52] | 20 wt.% loss in 10 days (in PBS, 37°C) [53] | |
Thermoset | Polyanhydarid (PA) | 3.39-3.49 [54] | 38.4 [54] | 85 wt.% loss in 7 days (in PBS, 37°C) [54] |
Poly(Glycerol sebacate) (PGS) | 1.2 [55] | 80-95 [55] | 22 wt.% loss in 30 days (in PBS) [56] |
기능성 필러에는 대표적으로 전기 전도성을 부여하기 위한 금속 필러와 유전 특성을 강화하기 위한 유전체 필러가 있다. 전기 전도성 금속 필러는 높은 전기 전도도를 가지며, 몰리브덴(Mo), 텅스텐(W), 철(Fe), 아연(Zn) 등이 포함된다. 복합체가 높은 전기 전도성을 띠기 위해서는 충분한 양의 금속 필러가 함유되어야 하는데, 이때 필러의 임계 함량을 침투 임계값(percolation threshold)이라고 한다. 침투 임계값보다 적은 양의 금속 필러가 함유되면 전기 전도 경로가 거의 존재하지 않아 복합체는 절연체의 특성을 띠는 반면, 금속 필러의 함량이 침투 임계값을 넘어서면 전기 전도 네트워크가 형성되어 전기전도도가 급격하게 증가하여 복합체는 전도체의 특성을 띤다(Fig. 1(c)) [19-22]. 금속 필러를 섞은 복합체를 활용한 변형률이나 수분을 측정하는 센서, 근거리 무선 통신(Near field communication, NFC) 장치, 그리고 인쇄회로기판(printed circuit board, PCB) 등의 보고되었다[20-24, 28-31]. Table 3는 현재 보고된 생분해성 기능성 복합체의 기능성 필러로 사용된 전기 전도성 금속 필러 물질들의 전기 전도도, 생분해 메커니즘, 그리고 응용 예시를 표로 정리한 것이다[20,23,28,30,58].
Fillers | Electrical conductivity (s/m) | Biodegradation mechanism | Application |
---|---|---|---|
Mo | 1.79×107 | 2Mo+2H2O+3O2→2H2MoO4 [58] | Strain sensor [20] |
W | 1.76×107 | 2W+2H2O+3O2→2H2WO4 [58] |
Moisture sensor [28] PCB board [30] |
Fe | 1.00×107 | Fe+2H2O→Fe(OH)2+H2 [58] | - |
Zn | 1.69×107 | Zn+2H2O→Zn(OH)2+H2 [58] | NFC device [23] |
유전체 필러는 높은 유전 상수를 가지며, 이황화몰리브덴(MoS2), 이산화 규소(SiO2) 등이 포함된다. 복합체의 유전 상수는 유전체 필러의 함량의 증가에 따라 선형적으로 증가하는 모습을 보이며, 유전 손실 또한 증가하는 양상을 보인다[25,59]. 유전체 필러를 섞은 복합체를 활용하여 기존의 고분자 매트릭스보다 더 우수한 유전 성능을 가진 복합체들이 보고되었다[25-27]. Table 4은 현재 보고된 생분해성 기능성 복합체의 기능성 필러로 사용된 유전체 필러 물질들의 유전 상수와 생분해 메커니즘을 표로 정리한 것이다.
Fillers | Static dielectric constant | Biodegradation mechanism |
---|---|---|
SiO2 | 3.9 | SiO2+2H2O→Si(OH)4[60] |
MoS2 | 2.6~2.9 | 2MoS2+7O2→2MoO3+4SO2 MoS2+9/2O2+3H2O→MoO42−+2So42−+6H+[61] |
ZnO | 10.4 | ZnO+2H2O→Zn(OH)2 ZnO+H2O→Zn2++2OH− [62] |
복합체에서 기계적 물성의 향상이나 추가적인 특성이 필요한 경우, 첨가제를 통해 이를 달성할 수 있다. 가소제와 계면 활성제의 첨가를 통해 필러를 균일하게 분산시키거나 결합제를 통해 필러와 매트릭스를 화학적으로 결합시킴으로써 기계적 특성을 향상시킬 수 있다. 또한, 안정제를 통해 고분자의 분해를 방지하거나 난연제를 통해 타는 것을 방지하는 등 첨가제를 통해 복합체의 안정성도 향상되었다[63-64]. 이 중 가소제가 생분해성 복합체에서 주로 사용되었으며, 가소제는 고분자 매트릭스와 기능성 필러 간의 윤활제로 작용하여 기능성 필러가 고분자 매트릭스 사이로 균일하게 분포할 수 있도록 도와주며, 이를 통해 기계적 특성을 향상시키고 변형에 대한 전기 전도성의 감소를 줄이는 역할을 한다. 특히, 금속 필러가 함유된 전기 전도성 복합체에서 필러의 분포가 불균일하면 장거리 전기 전도 경로 생성이 어려워 임계 침투값이 증가하기 때문에, 가소제의 첨가를 통한 필러의 균일성 확보는 매우 중요하다. 테트라글라이콜(tetraglycol, TG), 글리세롤(glycerol), 소르비톨(sorbitol) 등의 가소제가 생분해성 기능성 복합체에 사용된 것으로 보고되었다[19,20,22].
전기 전도성 재료는 전자 소자에서 전기 신호를 효율적으로 전달하고 전기적인 신호를 보호하는 역할을 한다. 소자의 회로 내에서 전기 신호를 전달하기 위해 전도성 재료가 필요하며, 서로 다른 회로나 소자를 전기적으로 연결해주는 전도성 연결에도 전도성 재료가 사용된다. 또한, 온도나 압력 등 외부의 물리적인 변화를 감지하여 전기 신호로 변환하는 장치인 센서에서도 전도성 재료가 필요하다. 따라서 생분해성 전기 전도성 복합체는 생분해성 유연전자소자에서 필수적인 재료이다. 생분해성 전기 전도성 복합체는 생분해성 고분자 매트릭스와 생분해성 금속 필러로 구성되어 있으며, 금속 필러들이 전기 전도성 경로를 형성함으로써 전기 전도성을 가지는 특성을 가진다. 금속 필러의 비율이 증가함에 따라 전도성 경로가 많아져 전기 전도성은 증가하지만, 동시에 취성이 증가하는 등 유연소자에 적합하지 않은 기계적 특성을 가지게 된다[19-21,23-24]. 따라서 기계적 특성을 향상시키거나 전기 전도성을 향상시키는 방법에 대한 다양한 연구들이 진행되고 있으며, 복합체 구성 요소의 재료의 변경과 금속 입자의 소결 등의 방법들이 보고되었다[20,22-24].
생분해성 전기 전도성 복합체의 금속 필러 재료에는 Mo, W, Fe, Zn 등의 생분해성 금속들이 사용되어 왔다[20-24,28-30]. Fig. 2(a)는 이러한 다양한 생분해성 금속을 필러로 활용하여 제작한 생분해성 전기 전도성 복합체들의 금속 필러의 부피 비율에 따른 전기 전도성을 측정한 결과이다[21]. 고분자 매트릭스로는 PA계열의 폴리-뷰테인다이싸이올 펜테노익 언하이드라이드(poly-buthanedithiol pentenoic anhydride, PBTPA)가 사용되었다. 금속 필러의 부피 비율이 증가함에 따라 침투 이론(percolation theory)에 따라 전기 전도성이 증가하는 양상이 나타났다[21]. 이는 필러의 양이 많아짐에 따라 전기 전도성 경로들이 강화되었기 때문이다[19]. 하지만 필러의 양과 전기 전도성이 무조건적인 상관관계를 갖는 것이 아니라, 필러의 양이 특정 값을 초과하면 필러가 첨가됨에 따라 오히려 전기 전도성이 감소하게 된다. 필러의 양이 과하게 많아지면 복합체 내 고분자의 상대적인 양이 감소하여 치수 축소(dimensional shrinkage) 효과가 감소하고, 동시에 바인더의 적용 범위가 감소한다. 이에 따라 고분자 매트릭스 내에 필러가 불균일하게 분산되고, 따라서 전기 전도성이 감소한다[20].
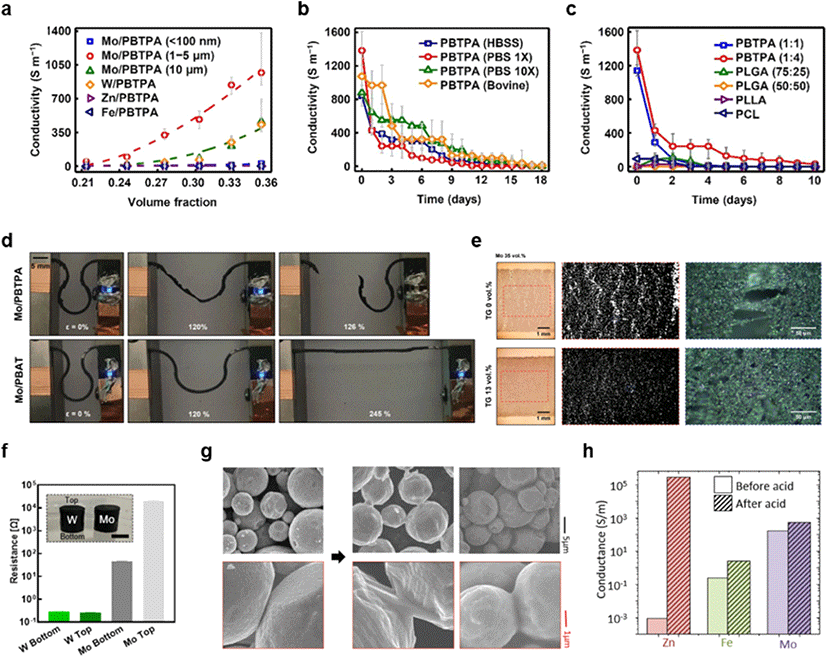
필러의 크기와 재료 또한 전기 전도성에 영향을 주었다. Mo/PBTPA 복합체의 경우, Mo 입자의 직경 크기가 1~5 µm인 복합체가 가장 높은 전기 전도성을 보였으며, 직경 크기가 10 µm 미만인 복합체와 100 nm 미만인 복합체 순으로 전기 전도성이 감소하였다. 또한, 고분자 매트릭스로 PBTPA를 사용하며 10 µm 미만의 크기를 가지는 다양한 금속 필러를 활용하여 복합체를 만든 경우, Mo/PBTPA와 W/PBTPA는 유사한 전기 전도성을 보인 반면, Zn/PBTPA와 Fe/PBTPA는 금속 필러의 낮은 전기음성도에 따른 비전도성 표면 산화층의 생성으로 인해 상대적으로 낮은 전기 전도성을 보였다[21]. 동일한 금속 재료를 사용한 경우에도 초기 표면 산화층의 두께나 필러의 형태가 복합체의 전기 전도성에 영향을 준다고 보고되었다[21,23]. 필러의 표면 산화층이 두꺼울수록 복합체 내 전도성 경로가 약화돼 전기 전도도가 감소한다. 또한, 0D, 2D, 그리고 3D 형태의 필러보다 1D 형태의 필러가 이방성 구성과 방향성의 용이성으로 인해 인접한 필러들과 더 잘 접촉할 가능성이 있으며, 따라서 적은 양으로도 높은 전기 전도성을 부여한다[19].
Fig. 2(b) 및 Fig. 2(c)는 생분해성 전기 전도성 복합체의 용해 거동을 분석한 결과이다[21]. Fig. 2(b)에서는 Mo/PBTPA(1~5 µm, 35 vol% Mo)를 37°C의 pH 7.4의 인산완충생리식염수(phosphate-buffered saline, PBS) 용액, Hanks의 균형 염 용액(Hank’s balanced salt solution, HBSS), 소 태아 혈청(bovine serum)에 생분해시킨 시간에 따른 전기 전도도를 측정한 결과로, 다양한 용액에 따른 생분해능을 나타냈다. Fig. 2(c)는 Mo 필러(1~5 µm)를 PBTPA, 폴리락테이트-코-글라이클레이트(Polylactic-co-glycolic acid, PLGA), 폴리- L-젖산(poly-L-lactic acid, PLLA), PCL에 분포시켜 제작한 복합체(35 vol% Mo)들을 37°C의 PBS 용액에 생분해시킨 시간에 따른 전기 전도도를 측정한 결과로, 동일한 금속 필러를 사용했음에도 고분자 매트릭스의 종류에 따라 전기 전도성이 달라질 수 있음이 확인되었다.
생분해 시간이 증가함에 따라 복합체의 전기 전도성은 감소하는 양상을 보였다[20-24]. 이는 고분자 매트릭스가 스웰링 및 분해됨에 따라 바인더의 역할을 충분히 수행하지 못하여 전도성 금속 필러의 손실이 발생하거나, 금속 필러가 분해됨에 따라 필러의 부피 비율이 감소하여 전기 전도성 경로가 약화되기 때문이다[19]. 친수성이 큰 고분자일수록 수분 침투, 스웰링 및 고분자 분해가 빠르게 일어나 전도성 필러의 손실이 커져 전기 전도성 감소율이 증가하는 것이 확인되었다[21]. 소수성이 크고 분해가 느린 고분자의 경우, 필러의 분해로 인한 전기 전도성 변화가 주요하게 작용하였는데, 분해 초기 단계에서는 금속 필러의 표면 산화층이 먼저 분해되어 전도성 향상이 확인되었으며, 그 후 점진적인 필러의 부피 비율 감소로 인해 전기 전도성이 감소함이 확인되었다[20,22]. 표면 산화층을 제거한 경우, 분해 초기의 전도성 향상이 나타나지 않았으며, 지속적인 감소만이 보고되었다[20]. 또한, 고분자와 필러의 분해로 인한 필러 부피 비율 감소 외에도, 생분해 과정 중 발생하는 복합체의 균열 또한 전기 전도성 감소의 원인으로 확인되었다[22].
유연성, 신축성 등 유연소자에 적절한 기계적 특성을 가지게 하기 위한 전략으로 고분자 매트릭스를 더 유연하고 신축성 있는 재료로 변경하거나 가소제를 첨가하여 금속 필러들을 더 균일하게 분산시키는 방법 등이 보고되었다. Fig. 2(d)는 고분자 매트릭스 재료를 PBTPA에서 PBAT로 변경함으로써 복합체의 기계적 특성을 개선시킨 예시이다[20]. Mo/PBTPA(35 vol% Mo)와 Mo/PBAT(35 vol% Mo)를 구불구불한 구조로 제작하여 힘을 주어 당겨본 결과, Mo/PBTPA는 126%의 변형률에서 끊어진 반면, Mo/PBAT는 245%의 변형률에서도 끊어지지 않고 형태와 전기 전도성이 유지되었다. Fig. 2(e)는 가소제의 첨가를 통한 기계적 특성의 향상을 보여주는 예시로, 가소제 TG의 첨가를 통해 필러들이 더 균일한 분포를 가지게 되었고, 이에 따라 유연성과 신축성이 향상되었다. TG가 첨가되지 않은 Mo/PBAT 복합체는 20%의 인장 변형률에서 국부적이고 큰 균열이 발생한 반면, Mo/TG/PBAT 복합체는 균일하게 분산된 작은 균열이 발생하였다.
전기적 특성을 향상하기 위한 전략으로 복합체 재료를 변경하거나 금속 필러를 소결하는 방법 등이 보고되었다[20,22,23]. 복합체 내에서 필러의 분산은 제타 전위, 입체적 안정화, 습윤성 및 표면 형태 등의 요소에 의해 결정되고, 이에 따라 적절한 재료를 선택하면 균일한 전도성 경로를 지닌 전도성 복합체를 형성할 수 있다[22]. Fig. 2(f)는 고분자 매트릭스는 비즈 왁스로, 금속 필러를 Mo에서 W으로 변경함으로써 전기 전도성을 향상시킨 예시로, 복합체 재료의 변경에 따른 균일한 분포를 통한 등방성 전도성이 확인되었고 표면 저항의 감소하였다.
Fig. 2(g) 및 Fig. 2(h)는 전기화학적 소결을 통해 전기 전도성을 향상시킨 예시이다[23]. Zn 입자를 완충 산성 용액에 넣으면, 자연 발생 산화층이 용해되고, Zn/H2O 경계에서 Zn와 Zn2+이 자체 교환되면서 전기화학적 소결이 발생하여 결과적으로 전기 전도성이 향상된다[23]. Fig. 2(g)는 Zn 입자를 CH3COOH/H2O 용액에 넣어 전기화학적으로 소결한 주사전자현미경 사진으로, 입자들의 소결이 진행되었음이 확인되었다. Fig. 2(h)는 고분자 매트릭스가 폴리비닐피로리돈(polyvinylpyrrolidone, PVP)인 Zn, Fe, Mo 복합체의 산처리 유무에 따른 전도성 측정 결과이다. 표준 환원 전위가 작은 금속일수록 두꺼운 자연 산화물을 형성하는 경향으로 인해 산처리가 되지 않은 전도도의 상대적인 값은 Zn<Fe<Mo로 나타났다. Fe와 Mo는 Zn와 달리 Fe2+와 Mo3+를 환원하는 것보다 H+를 환원하는 것을 선호하기 때문에 산처리 후 Zn/PVP 복합체는 전기 전도성 향상이 크게 일어난 반면, Fe/PVP와 Mo/PVP는 상대적으로 전도성이 적게 향상되었다.
유전체는 외부 전기장의 존재 하에서 분극을 통해 전기 에너지를 저장할 수 있는 재료로, 축전기에서 전기용량과 최대 동작 전압이 증가시키기 위해 사용된다. 또한, 유전체는 트랜지스터와 같은 전자 부품에서 인접한 금속과 반도체 간의 용량 결합(capacitive coupling)을 향상시키고, 전극 사이의 누설 전류를 억제하기 위한 절연체로 사용되는 중요한 재료이다. 따라서 생분해성 유전체 복합체는 생분해성 전자소자에서 활용가능성이 매우 높은 중요한 재료이다. 유전체 복합체는 고분자 매트릭스와 유전체 필러로 구성되어있으며, 전기장이 가해지면 필러와 매트릭스 사이의 경계에서 미시적인 쌍극자가 형성되는 원리로 유전 성능이 향상된다[59,65]. 이러한 유전체 복합체는 유전 성능이 낮은 순수 고분자의 단점을 보완하며, 최근 보고되고 있는 생분해성 유전체 복합체들은 추후 다양한 유전체 재료가 생분해성 소자에 활용될 수 있음을 시사한다.
생분해성 유전체 복합체의 필러 재료에는 SiO2, MoS2, 산화아연(ZnO) 등의 생분해성 재료들이 사용되어 왔다[25-27]. Fig. 3는 생분해성 유전체 복합체의 예시로, 키틴(chitin) 매트릭스에 MoS2를 첨가함으로써 유전 성능을 강화하였다[25]. Fig. 3(a)는 필러의 함량에 따른 복합체의 단면의 주사전자현미경 사진으로, 왼쪽에서 오른쪽으로 갈수록 필러의 함량이 증가한다. 각각의 사진은 0, 1, 5, 7 wt%의 MoS2 필러를 함유하였다. Fig. 3(b)는 필러의 함량에 따른 복합체의 유전 성능을 나타낸 결과이며, 각 샘플명 뒤에 붙은 숫자는 필러의 무게 비율을 의미한다(e.g., RCH-MoS2 1:1 wt%의 MoS2 필러를 포함). 필러가 많이 포함될수록 유전 상수(dielectric constant)는 증가하였지만, 동시에 유전 손실(dielectric loss)도 일반적으로 증가하는 양상을 보였다. Fig. 3(c)는 순수 chitin 고분자와 MoS2/chitin 복합체로 각각 얇은 막을 제작하여 분석한 결과로, 순수 chitin 막이 2.17 Jcm−3의 방전 에너지 밀도를 보인데 비해 MoS2/chitin 막은 4.91 Jcm−3의 방전 에너지 밀도를 보이며 2배 이상의 향상이 확인되었다.
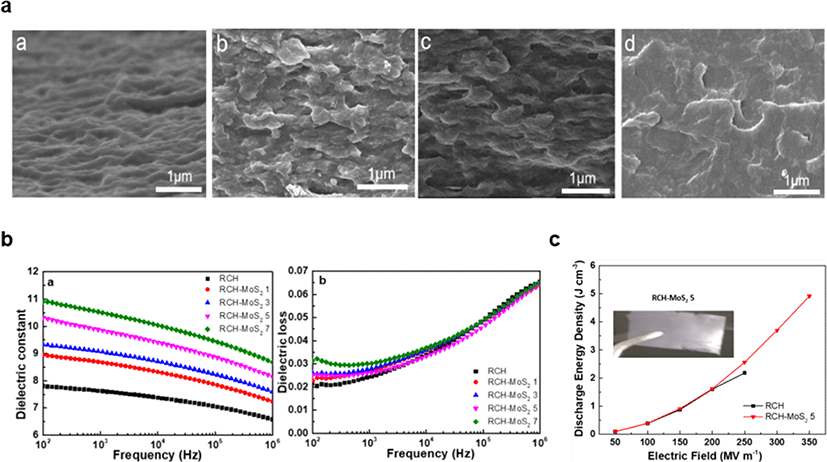
복합체 인쇄 및 제작 기술은 필요한 기계적 및 기능적 특성을 갖는 복잡한 소자를 생산하는데 사용되기 때문에 매우 중요하다. 생분해성 기능성 복합체를 활용하여 전자소자를 제작하기 위해서는 3D 프린팅, 스크린 프린팅, 주조 등의 방법으로 액체 상의 복합체를 원하는 모양으로 인쇄 및 성형한 후, 고체 상으로 응고시키는 과정이 필요하다. 복합체가 고체 상으로 응고되는 과정의 방법, 시간 등에 따라 소자의 물성과 구조가 바뀔 수 있기 때문에, 필요한 특성에 따라 적절한 경화 방식을 선택해야 한다[66-67]. 생분해성 기능성 복합체 분야에서는 용제 주조(solvent casting), 용융 성형(melt molding), 광중합(photopolymerization) 등의 응고 방법이 보고되었다[19-23,28-29].
용제 주조는 복합체를 구성하는 고분자 매트릭스를 적절한 유기 용매에 용해시키고, 원하는 구조로 인쇄 및 성형한 후, 용매를 증발시키는 방식으로 소자를 제작하는 기술이다. Fig. 4(a)는 3D 프린팅으로 소자를 인쇄하고 용제 주조 방식으로 소자를 제작하는 과정과 그 결과로 제작된 소자들 중 대표적인 예시인 W/PLA 정전식 수분 센서이다[28]. 용제 주조 방식은 단순하고 저렴하며, 다양한 유기 용매를 사용하여 다양한 종류의 고분자 기반 복합체를 인쇄할 수 있다는 장점이 있다. 하지만 여러 고분자로 구성된 복합체를 인쇄하기 어렵고, 유기 용매가 잔류하거나 용매의 제거 과정에서 복합체의 구조가 일부 변형될 수 있다는 단점이 존재한다. 용매의 양에 따라 제작되는 소자의 특성도 변화하는데, 일반적으로 용매의 양이 많을수록 소자에 기공이 많아지고 이에 따라 기계적 강도가 감소하며 전기적 특성도 영향을 받는다고 보고되었다[68-69].
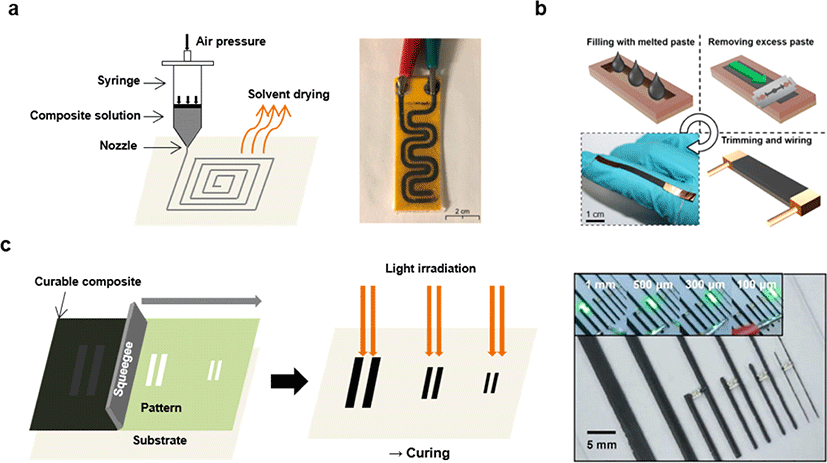
용융 성형은 복합체를 구성하는 고분자 매트릭스의 녹는점 이상으로 온도를 올려 고분자를 녹이고, 원하는 구조로 성형한 후, 온도를 다시 낮춰 굳히는 방식으로 소자를 제작하는 기술이다. Fig. 4(b)는 용융 성형 방식을 이용한 소자의 제작 과정과 그 결과로 제작된 W/Beeswax 저항 센서이다[22]. 용융 성형은 다양한 고분자로 구성된 복합체도 쉽게 성형할 수 있으며, 고밀도로 밀집된 고분자를 형성할 수 있어 높은 기계적 강도와 내구성을 가진 제품을 얻을 수 있다는 장점이 있다. 하지만, 열가소성 고분자로 구성된 복합체에만 활용할 수 있으며, 고온에서 고분자 매트릭스나 기능성 필러가 손상될 수 있다는 단점이 존재한다[22]. 또한, 높은 용융 온도를 유지하기 위한 특수 장비가 필요하다는 한계점도 있다.
광중합 방식은 액체 상의 복합체를 성형한 후, 빛을 사용하여 경화시키는 기술이다. Fig. 4(c)는 스크린 프린팅을 통해 인쇄한 복합체를 광중합 방식으로 경화시키는 과정과 그 결과로 제작된 Mo/PBTPA 복합체이다[21]. 광중합 방식은 빠른 경화 속도와 높은 반응 효율 덕분에 빠르게 소자를 제작할 수 있다는 장점이 존재하지만, 광 활성화 고분자로 구성된 복합체에만 활용할 수 있다는 단점이 있다[19,21].
다양한 방법으로 인쇄된 복합체를 용제 주조, 용융 성형, 그리고 광중합 등의 방법을 통해 응고시킴으로써 소자의 일부를 생분해성으로 대체하거나 모든 부분을 생분해성으로 구성하여 친환경 유연전자소자 혹은 생분해성 체내 삽입형 소자를 제작하려는 연구가 활발하게 진행되고 있다. 이에 따라 전기적 특성을 부여할 수 있는 생분해성 기능성 복합체가 많은 관심을 받고 있고, 전도성 연결, 저항 기반 센서, 근거리 무선 통신 장치, 그리고 인쇄회로기판 등 다양한 생분해성 전자소자들의 제작이 보고되었다[20-24,28-31].
다양한 구성 요소로 이루어진 전자 소자에서 구성 요소들을 전기적으로 연결해주는 전도성 연결과 휘어짐, 온도 변화 등의 외부 자극에 따라 저항이 변화하는 저항 센서들이 전도성 복합체의 간단한 데모로 보고되었다. Mo/PBTPA, Mo/PBAT, Mo/cellulose, W/Beeswax 등 다양한 생분해성 전도성 복합체로 전도성 연결과 저항 기반 센서가 제작되었다[20-22,24,31]. Fig. 5(a)는 생분해성 전도성 연결의 예시로, Mo/PBTPA 복합체를 Mg 코일에 연결하여 무선으로 전력을 전달받아 LED를 작동시킨 결과를 나타낸다[21]. Fig. 5(b)는 W/ Beeswax 복합체로 제작한 저항 기반 굽힘 센서와 온도 센서이다[22]. 센서가 부착된 손가락을 구부리면 센서의 저항이 감소하고 손가락을 펴면 저항이 증가하는 것이 확인되었으며, 각 상태에서의 저항은 일정하게 유지되었다. 일반적으로는 굽힘 운동이 저항을 증가시
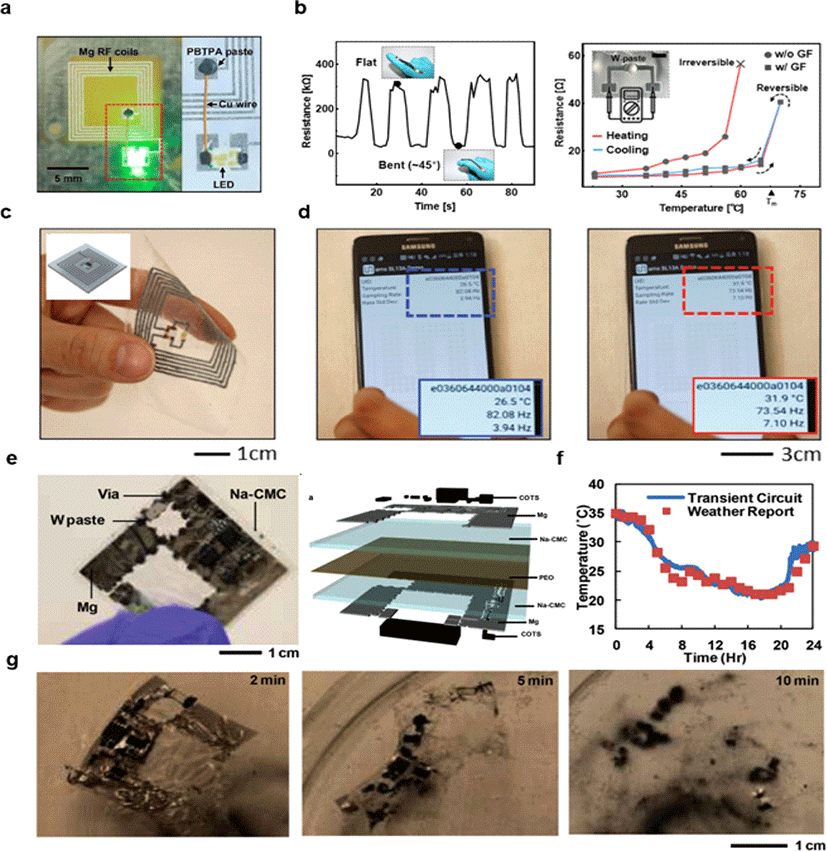
키는 것과 반대 양상이 나타났으며, 이는 굽힘에 의해 수직 압축을 생성하여 입자들 간의 거리가 감소되었고, 이에 따라 W 입자들이 더 가까워져 터널링 저항을 감소시켰기 때문이다[20,22]. 이 현상은 Mo/ PBAT로 제작한 굽힘 센서에서도 동일하게 나타났다[20]. 온도 센서의 경우, 가소제 글라이코퓨롤(glycofurol, GF)가 첨가된 복합체로 제작된 온도 센서는 외부 온도의 증가와 감소에 따라 저항이 변화함이 확인되었으며, 가열과 냉각 과정에서 온도에 따른 저항이 거의 일치하였다. 가소제가 첨가되지 않은 복합체는 온도가 용점점을 초과할 때 영구적으로 전기 전도성을 잃었다. 이 외에도 저항 기반 압력 센서, 정전식 감응 수분 센서 등의 여러 센서들이 제작되었으며, 전류로 발열을 발생시키는 줄 히터(Joule heater)도 간단한 데모로 보고되었다[20].
생분해성 복합체를 활용한 근거리 무선 통신 장치의 개발도 확인되었다. Fig. 5(c)는 Zn/PVP 복합체를 스크린 프린팅하여 제작한 무선 주파수(radio frequency, RF) 안테나에 NFC 칩을 부착하여 제작한 NFC 장치이다[23]. Fig. 5(d)는 NFC 장치와 스마트폰을 이용하여 무선으로 온도를 측정한 결과로, 온도 증가를 성공적으로 측정하였으며, 이 외에도 외부 RF 소스로부터 무선으로 전력을 수급 받거나 웹 사이트를 자동으로 시작하는 기능도 확인되었다[23]. Zn/PVP 기반 NFC 장치를 100 µm 두께의 PLGA로 코팅하고 물에 담가 분해시킨 결과, 몇 시간 동안은 흔들림 없이 기능을 유지하는 것이 확인되었으며, 수 일 후에 수소 거품의 발생이 시각적으로 확인됨을 통해 Zn의 분해를 확인하였다. 이외에도 Mo/PBAT, W/Beeswax, W/PEO 등의 재료를 활용하여 무선 전력 수신 코일이 개발되었다[20,22,30].
생분해성 전도성 복합체를 다른 생분해성 재료와 함께 활용하여 개발한 전자소자도 보고되었다. Fig. 5(e)는 W/PEO 복합체를 활용하여 제작한 생분해성 인쇄회로기판의 모습과 구조이다. 인쇄회로기판에서 W/PEO 는 상용 기성품 칩과 Mg 기판을 전기적으로 연결하며 물리적으로 고정하는 데에 사용되었으며, 우수한 기계적 강도 덕분에 반복적인 구부림에도 접착이 유지되었다[30]. Fig. 5(f)는 생분해성 인쇄회로기판을 활용하여 온도를 측정하고 무선으로 전송된 온도 데이터를 지역 날씨 보고서의 데이터와 24시간 간격으로 비교한 결과로, 높은 정확도를 보였다. Fig. 5(g)는 인쇄회로기판이 물에서 생분해되는 과정을 나타낸 것으로, 상용 기성품 칩과 트랜지언트 금속을 제외한 모든 구성 요소들이 10분 내에 분해되었으며, 수 시간 후 트랜지언트 금속들에서도 분해 시작의 초기 반응이 확인되었다[30].
기능성 복합체는 고분자 매트릭스에 기능성 필러를 첨가하는 방법으로 형성되며, 기능성 필러의 종류, 크기, 함량 등에 따라 복합체의 기능성이 결정된다. 일반적으로 필러의 함량이 증가함에 따라 복합체의 기능성이 강화 및 향상되지만, 동시에 복합체의 기계적 물성은 악화된다[19-24]. 이는 필러들이 응집하여 응력 집중체(stress concentrators)로 작용하여 복합체의 결함을 유발하고, 이러한 결함들이 인장 강도와 연신율을 감소시키고 취성을 증가시키는 등 기계적 물성을 악화시키기 때문이다[71]. 유연전자소자의 다양한 활용을 위해서 우수한 기계적 물성은 필수적이고, 따라서 높은 기능성과 우수한 기계적 물성을 가지기 위한 개선 방법들이 보고되었다[19-22,72-73].
복합체에 가소제를 첨가함으로써 필러들을 균일하게 분포시켜 응집을 막을 수 있고, 이를 통해 기계적 물성을 향상시킬 수 있다[19-22]. Mo/TG/PBAT는 가소제 첨가를 통해 기계적 물성을 향상시킨 예시로, Mo/PBAT(35 vol% Mo)에 TG(6.5 vol%) 를 첨가한 결과, 연신율이 36.4%에서 67.8%로 증가하며 1.86배의 향상을 보였다[20]. 이는 TG의 첨가를 통해 Mo 입자-Mo입자, Mo 입자-PBAT 고분자, PBAT 고분자-PBAT 고분자 간 마찰이 감소하여 Mo 입자들이 균일한 분포를 가지고, 이에 따라 PBAT 고분자의 움직임이 향상되었기 때문이다[20]. 하지만, 가소제의 함량과 복합체의 물성 개선이 완전히 비례하지는 않는다. TG가 19.5 vol% 첨가된 경우에는 6.5 vol% 첨가된 경우보다 오히려 연신율이 감소하였다[20]. 이는 PBAT 고분자의 함량이 낮아져 바인더의 역할을 충분히 하지 못하였기 때문이다[20].
가소제 첨가를 통한 기계적 물성의 향상은 W/GF/ Beeswax 복합체에서도 확인되었다[22]. W 입자 표면의 산화물은 친수성인 반면, Beeswax 매트릭스는 소수성이다. 이러한 습윤성(wettability) 차이로 인해 두 성분은 낮은 접착력을 가지며, 이에 따라 W/Beeswax 복합체는 필러 입자가 균일하게 섞이기보다는 응집하는 경향을 보인다[22]. 따라서 W/Beeswax 복합체에 첨가된 GF는 계면활성제 역할을 함으로써 습윤성 차이를 감소시키고, 이에 따라 필러가 균일하게 분산되며, 결과적으로 내부 응력이 감소하여 기계적 물성 향상된다[22]. 이와 같이 가소제 첨가를 통해 기계적 물성 개선을 시키는 전략이 현재 생분해성 기능성 복합체에서 유효하게 작용되고 있다.
생분해성 금속 나노와이어(nanowire), 나노로드(nanorod) 등 다양한 형태의 생분해성 기능성 필러 재료의 개발이 시도되고 있음에 따라, 단일 필러가 아닌 다양한 종류의 필러를 활용하여 복합체 내부의 필러 구조에 변화를 줌으로써 기계적 물성을 향상시키는 방식 또한 추후에는 생분해성 기능성 복합체에 적용이 가능할 것이라고 예상된다. 1D, 2D 등 다양한 형태의 필러들을 입자 형태의 필러들과 섞어서 사용함으로써 구조적 해상도를 향상시키는 방법이 다양한 복합체 연구에서 보고되고 있으며, 특히 이방성과 방향성을 가져 적은 함량으로도 높은 기능성을 부여하는 1D 형태의 필러를 사용하는 연구가 많이 진행되었다[19,72-73]. 1D 형태의 탄소 나노튜브와 입자 형태의 카본 블랙을 PLA 고분자에 첨가하여 제작한 복합체의 경우, 더 적은 필러 함량으로도 카본 블랙만 활용한 복합체에 비해 더 뛰어난 전기전도성을 보였으며, 기계적 물성도 크게 향상되었다[72-73]. 생분해성 금속 나노와이어 등의 기능성 필러 재료의 개발을 통해 차후에는 이러한 구조적 해상도를 향상시키는 방법이 생분해성 기능성 복합체 분야에서 충분히 활용될 수 있을 것으로 기대되며, 이는 높은 기능성을 가지며 뛰어난 기계적 물성을 가지는 생분해성 기능성 복합체의 개발이 가능함을 시사한다.
3. 결론 및 전망
다양한 특성을 가지는 생분해성 전도성 복합체와 유전체 복합체들이 개발되었다. 전도성 복합체를 인쇄하여 제작한 전도성 연결, 센서, 인쇄회로기판 등의 다양한 활용 사례가 있었으며, 유전체 복합체의 예시들을 통해 향후 인쇄를 통한 전자 소자 제작 가능성이 확인되었다. 이는 향후 지속 가능한 친환경 전자소자에서 생분해성 기능성 복합체의 활용 가능성과 시사한다. 이러한 발전에도 불구하고, 여전히 생분해성 기능성 복합체에는 몇 가지 도전 과제가 있다. 기능성 필러는 명확하게 고분자 매트릭스에 기능성을 부여하거나 강화해주지만, 기계적 특성의 측면에서는 취성을 증가시켜 복합체를 작은 힘에도 깨지기 쉽게 만든다. 가소제 첨가 등의 다양한 방법을 통해 복합체의 특성이 개선되었지만, 여전히 유연소자에 적합한 기능성과 기계적 물성을 달성하는 것은 매우 중요한 이슈이다. 아직 생분해성 유전체 복합체를 활용하여 소자를 제작한 사례가 적기 때문에 유전체 복합체 기반 소자도 많은 부분 발전이 필요하다. 생분해되어 환경에 해를 끼치지 않는다는 점, 처리 비용이 적다는 점은 기존 유연전자소자들이 당면한 문제점을 해결한다는 부분에서 향후에 생분해성 유연전자소자가 미래 산업을 주도할 수도 있다는 가능성을 시사한다. 복합체 물성 향상 연구와 다양한 재료로 구성된 생분해성 복합체의 개발은 생분해성 기능성 복합체 기반 전자소자의 활용 영역을 더욱 확장시킬 것으로 기대된다.